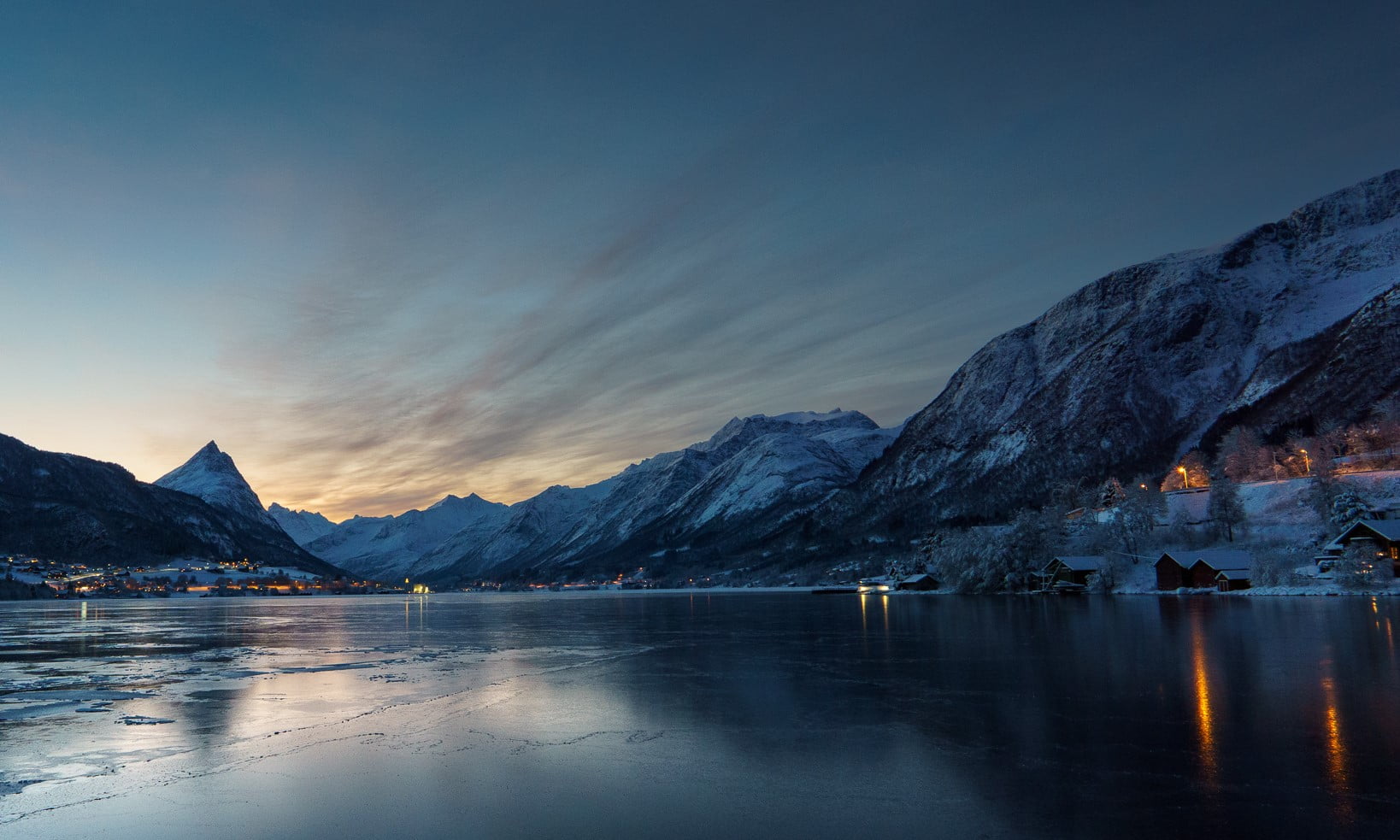
Carbon neutral company
Materiality analysis
Ekornes has devoted considerable resources in recent years towards increasing the focus on continuous improvement and has implemented numerous measures to reduce the company’s environmental impact.
New technologies, more environmentally friendly materials and new product solutions have resulted in one of the most efficient manufacturing environments in the furniture industry today. By engaging in sustainable production, the Ekornes Group reduces the environmental impact of its products measured over their entire lifespan. This contributes to a sustainable development of the products, as well as the Group as a whole. Anything that help increase quality or reduce wastage of raw materials, time and energy is a step in the right direction. We are now ready to step up our efforts.
Avfallshåndtering
Furniture production generates waste and Ekornes perceives it as a highly important environmental target to reduce the waste from its facilities. Efforts to reduce the volume of waste and to increase recycling are therefore important. Ekornes sorts all its waste at source in such a way that the bulk of the waste is reused, recycled or used for energy recovery at its own plants. For the Svane® and Stressless® factories, sorting and recycling accounted for 80 per cent of all recorded waste. This meets the current recycling target.
Ekornes has over time devoted resources to reduce the wastage from our production and have been able to lift the waste recycling percentage in the Norwegian and American factory to 80 per cent. This has been a target for the factories since 2015. We have now set an even more ambitious target of achieving > 90 per cent in the same plants by 2025. To achieve this, we seek to focus on the utility value from the byproducts from our production. We are also expanding the recycling target to an overall target of 100 per cent for the Group by 2030. To reach this, Ekornes welcomes collaboration partners to make it a joint effort.
To achieve its waste-reduction target, Ekornes monitors the volume of waste from its production facilities. Efforts are also made to increase the individual employee’s awareness in this area, so that everyone can contribute to target realization. Going forward, Ekornes will continue enhancing the waste focus in the facilities with a new and easier recycling system. The recycling system has been implemented at the Norwegian factories. Ekornes aims to implement this in the other factories in the following year.
Ekornes also generates waste outside of its direct production. In 2021, Ekornes became a member of the Atea 100% club, which is our IT-supplier Atea’s own initiative for enhanced reuse and recycle of IT-products. During 2021, Ekornes saved 11 025 kg CO2 equivalents through the Atea program. Of the collected units by the initiative, 43% were reused and 57% were recycled.
Climate impact
Ekornes works to reduce the total emissions from the group and its facilities. Our target since 2015 has been to reduce the Group’s GHG emissions from its own activities (scope 1 and 2) by 10%. By 2021, the Group has increased total Greenhouse gas emissions by 9%from 2015, primarily due to increased production from the Thailand factory, which has a different energy mix than the rest of the Group. This number also betrays the fact that the number of factories in the Group has increased substantially, with a corresponding rise in revenues. The GHG intensity, as measured by total annual GHG emissions divided by revenues, has been reduced by 31% in the same period. We have now set a new target of achieving a 55% reduction in scope 1 and 2 GHG emissions by 2030 from the 2015 level. Ekornes reports its greenhouse gas emissions in three “scopes”. For Ekornes, emissions in Scope 1 (direct emissions) come from internal transport, heating with natural gas and oil, as well as carbon dioxide released during polyurethane foam production. Scope 2 encompasses indirect emissions derived from the generation of third-party electricity. Scope 3 is associated with the treatment of waste, air travel and authorized business use of motor vehicles. This includes only parts of the Scope 3 emissions of the Group and Ekornes targets mapping more of the Scope 3 emissions in the full-cycle value chain in its reporting from 2022 and onwards.
One of Ekornes scope 3 emission factors has been business travels. In the past few years, Ekornes has had a strong focus on reducing the total greenhouse gas emissions from business travels and has implemented this in the Group’s travelling policy. The Covid-19 pandemic has naturally had an impact on the amount of business travel, but it has also shown that using technological solutions as a substitute for long distance travel is a perfectly viable way to maintain cooperation between the Group’s global locations, as well as with the business partners.
Ekornes monitor the direct emissions from the production. There are conducted emission measurements on an annual basis, to be compliant with local regulations. Direct emissions to air from the manufacturing process are primarily generated by oil and solid fuel boilers. Three of Ekornes’ Stressless factories are subject to licenses granted by the local County Governor. Ekornes also have diffuse emissions of diisocyanate gas and carbon dioxide from the production of polyurethane foam at factories in Norway, Lithuania, Thailand and Vietnam.
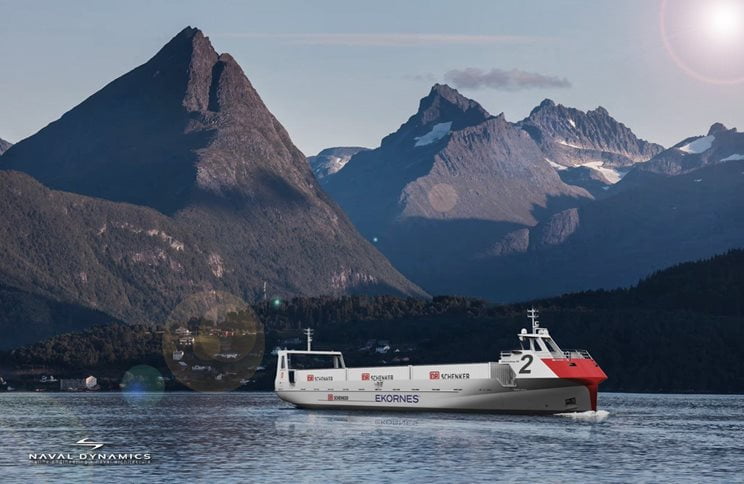
Grønn transportplan
Transport materially affects our carbon footprint. Ekornes has a goal to ship >70% of its outbound transportation on ships. Throughout 2021, Ekornes achieved 58% percent of the transportation from Ikornnes with ships. Long lead times to market led to a priority shift in transportation for central Europe during 2021. The aim of using sea transportation to reduce the total carbon footprint per produced seat and to reduce the impact on the road infrastructure. Externally, transportation locally in Norway is needed by road and Ekornes has, together with its transportation supplier DB Schenker, made an agreement to secure a biofuel transportation line between Oslo and Ikornnes, which will indirectly reduce our carbon footprint. According to plan, the biofuel transportation line will be effective from summer 2022. Internally, during 2021, Ekornes has received two electrical vehicles for internal transportation. These new vehicles which will go directly to reduce our local emissions. This is an inhouse fleet of vehicles to transport components between the factories.
Energieffektivitet
Our production facilities consume a high level of electricity in the production of our quality products. For all Ekornes production facilities in Norway, the energy consumed is based on 100% renewable hydropower. This has been certified in accordance with the EU Renewable Directive. Despite this, reducing electricity use is one of Ekornes’ main environmental objectives.
In 2015, we set a target to reduce the electricity consumption at the Norwegian and American production plants by 10% and we are pleased to report that we have received a reduction of 15% by 2021. Moving forward, with all plants included, we have raised the bar with a new goal to reduce the energy consumption per product with 40% before 2030 at all Ekornes plants.
All factories aim to implement renewable energy sources and to seek solutions to reduce overall energy use:
- During 2021, the Ekornes Thailand facility has worked on finding good solutions for solar cell power for the factory.
- Our factory in Lithuania holds an A+ energy certification, which has been achieved through use of geothermal energy, a high level of insulation and exterior use of LED and sensor-controlled lightening.
- The Group’s Norwegian plants primarily use bioenergy for heating. Woodchips, which is a by-product from the manufacturing process, constitute the primary energy source for heating at the factories on the northwest coast of Norway, while the Svane® plant at Fetsund uses a combination of woodchips, electricity and gas.
- The factory in Lithuania primarily uses geothermal heating.
- The factories in the USA, Thailand and Vietnam are less affected by ambient temperatures, and their energy consumption relates largely to their machine park.
- The use of daylight at the factories in Vietnam and Thailand has improved in the past year, which has reduced the need for artificial lighting.
- The factory at Fetsund has switched to LED lighting in its premises, which has also reduced energy consumption.
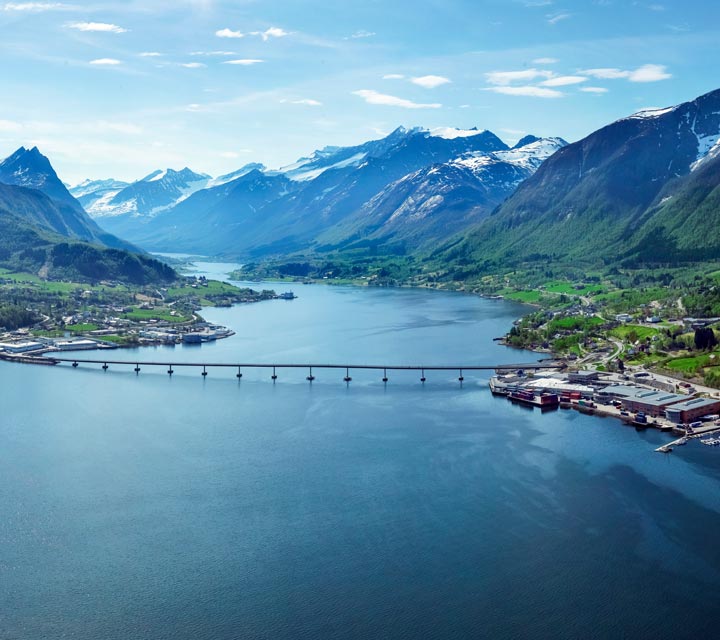
Water management
Stressless’ main facility is located at Ikornnes close to Sykkylvsfjorden. The company has therefore made discharges to water as a measurable parameter. Ekornes shall not have any unwanted incidents resulting in discharges to water. The production processes involving water consumption are performed in closed-loop systems. Discharges to water are normally channeled through our own and local authority waste treatment facilities, or it is delivered to an approved recipient. In recent years, the factories in Thailand and Vietnam have increased the recirculation of water from their surface coating facilities to reduce their overall water consumption. Water is an important resource for our production. Moving forward Ekornes will aim to measure its water consumption and set 2022 as baseline target.